News Center
Lets experience the speed of Sinotruk →
Data:2024-07-30 Source:SINOTRUK Pv:
I am now in the welding workshop of Sinotruk Laiwu Factory. What is welding? You can see the welding mask in my hand. We often see workers holding welding masks and welding with welding guns. Now the smart factory has replaced manual labor with robots. This model is made based on the prototype of the "New Yellow River" heavy-duty truck. When the parts enter the welding workshop, they are still pieces of steel plates, and when they go out, they are already the same as the front of the model. How is this process achieved? We will reveal it to you from the perspective of a cross-country drone.
After looking at so many processes, the most core one is the cab splicing process around us. Six robots work together, some carry parts and some weld, and the head is formed. The data is particularly worth mentioning: At present, the splicing accuracy of the key parts here is ±1mm, and the qualified rate has reached 100%, which shows the precision of the robot's work.
High-end and intelligentization bring about the liberation and development of productivity. The two production lines in our workshop only need 5 people to manage. In contrast, the photo in my hand is of the old welding workshop 4 years ago. The two production lines required about 400 people, and the current labor volume is only 1/80 of the past.
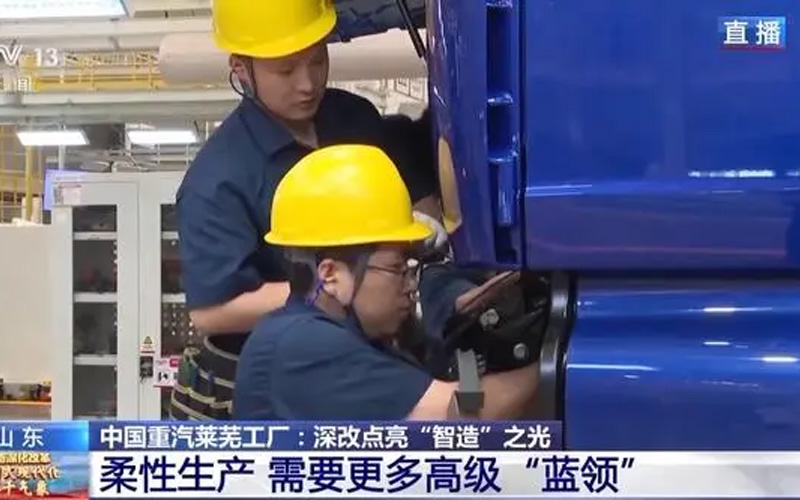
In recent years, China National Heavy Duty Truck Group has also been making full efforts in overseas markets. In the first five months of this year, China National Heavy Duty Truck Group's heavy-duty truck exports have exceeded 60,000 units, constantly breaking my country's monthly heavy-duty truck industry export record.
News
Latest News
- 【SINOTRUK GROUP】Sinotruks factories have achieved a "new speed" in development08-29-2025
- 【SINOTRUK HOWO】Permanent Secretaries or High-Level Representatives of the Ministries of Foreign Affairs of Nine Caribbean Countries08-22-2025
- Shandong Heavy Truck uses digital transformation as an engine to lead high-quality development08-04-2025
- Shandong Heavy Trucks full range of products supports the construction of the Yarlung Zangbo River super hydropower project07-25-2025
- Various media focus on Shandong Heavy Industry Group in the first half of the operating results to a new high07-21-2025
- Sinotruk Group Holds A Meeting To Celebrate The 104th Anniversary Of The Founding Of The Communist Party Of China07-04-2025
- Sinotruk Group Organization Of The “Virtue, Diligence And Integrity” Integrity Culture Joint Learning Activity06-23-2025